Reliably prevent costly production errors
The transition from engineering design to production planning is complex and labor-intensive. A significant challenge is accurately transferring changes from the engineering bill of materials (eBOM) to the manufacturing bill of materials (mBOM), a process often poorly supported by ERP systems. This increases the risk of errors. CONTACT Elements xBOM helps your company eliminate those failures in mBOM derivation from the eBOM – preventing expensive production errors before they occur.
Benefits of xBOM
- Optimize collaboration between engineering and production planning
- Quickly and reliably resolve quantity differences between eBOM and mBOM
- Synchronize bills of materials for service, spare parts, and maintenance to ensure data consistency
- Securely eliminate 3D model discrepancies
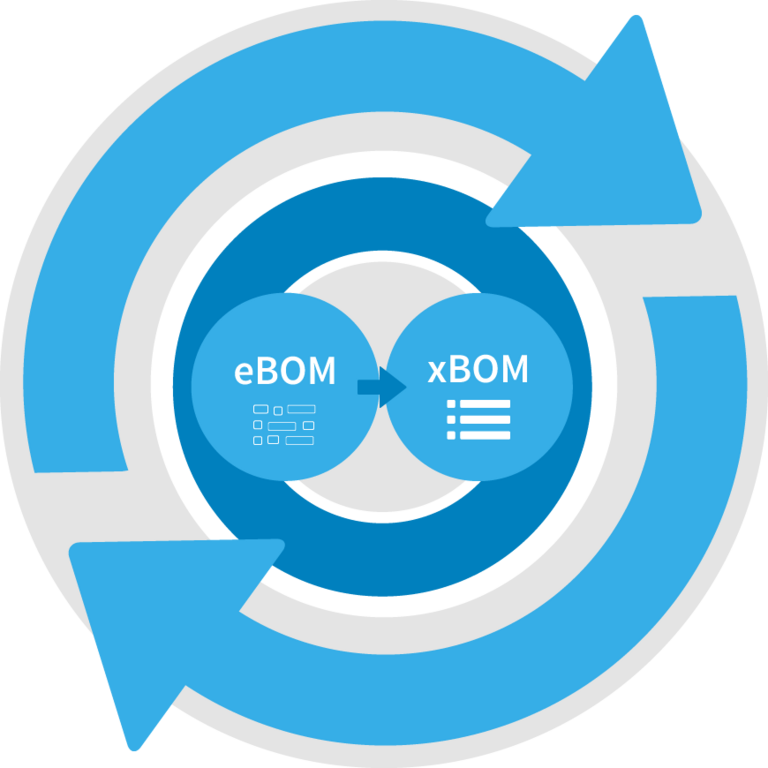
Interlock engineering and production planning
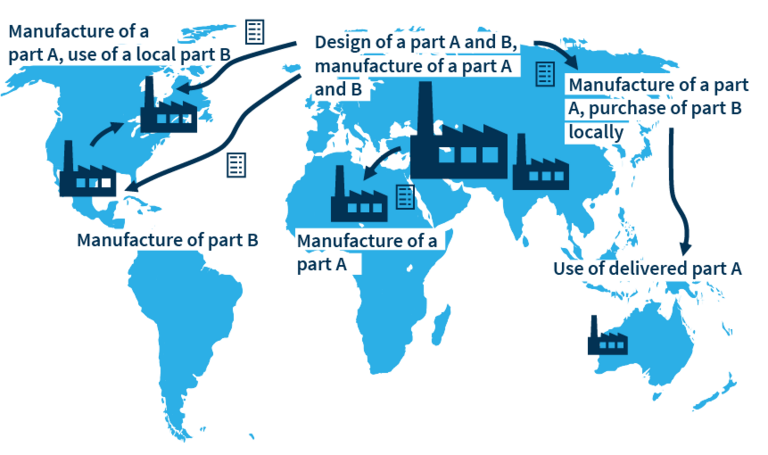
The central production planning provides site- or order-specific manufacturing bills of materials (mBOMs) for distributed plants. A seamless transfer of engineering changes to the mBOM is therefore crucial for collaboration with product development. The xBOM Manager facilitates this transition by ensuring the reliable synchronization of bill of material changes, taking into account both plant-specific and cross-plant requirements.
Interlock engineering and production planning
The central production planning provides site- or order-specific manufacturing bills of materials (mBOMs) for distributed plants. A seamless transfer of engineering changes to the mBOM is therefore crucial for collaboration with product development. The xBOM Manager facilitates this transition by ensuring the reliable synchronization of bill of material changes, taking into account both plant-specific and cross-plant requirements.
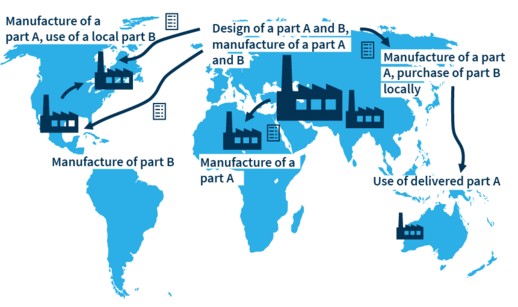
The central production planning provides site- or order-specific manufacturing bills of materials (mBOMs) for distributed plants. A seamless transfer of engineering changes to the mBOM is therefore crucial for collaboration with product development. The xBOM Manager facilitates this transition by ensuring the reliable synchronization of bill of material changes, taking into account both plant-specific and cross-plant requirements.
Eliminate quantity differences between eBOM and mBOM
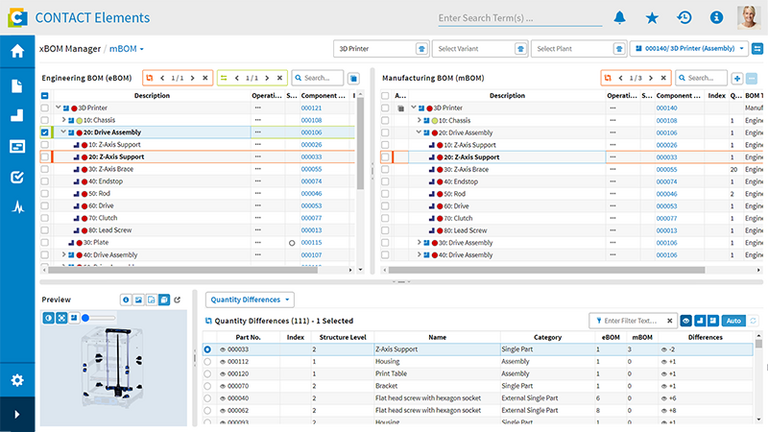
The xBOM Manager ensures rapid and secure bill of materials reconciliation. A key feature is the identification and resolution of quantity discrepancies, which are visually highlighted in the product structures. Users can navigate directly to the source of the difference. Structural changes in the eBOM, including modifications welding or assembly groups, are effortlessly transferred to the mBOM using drag & drop and intuitive integrated dialogs as part of the engineering change process.
Eliminate quantity differences between eBOM and mBOM
The xBOM Manager ensures rapid and secure bill of materials reconciliation. A key feature is the identification and resolution of quantity discrepancies, which are visually highlighted in the product structures. Users can navigate directly to the source of the difference. Structural changes in the eBOM, including modifications welding or assembly groups, are effortlessly transferred to the mBOM using drag & drop and intuitive integrated dialogs as part of the engineering change process.
The xBOM Manager ensures rapid and secure bill of materials reconciliation. A key feature is the identification and resolution of quantity discrepancies, which are visually highlighted in the product structures. Users can navigate directly to the source of the difference. Structural changes in the eBOM, including modifications welding or assembly groups, are effortlessly transferred to the mBOM using drag & drop and intuitive integrated dialogs as part of the engineering change process.
Synchronize any BOM type
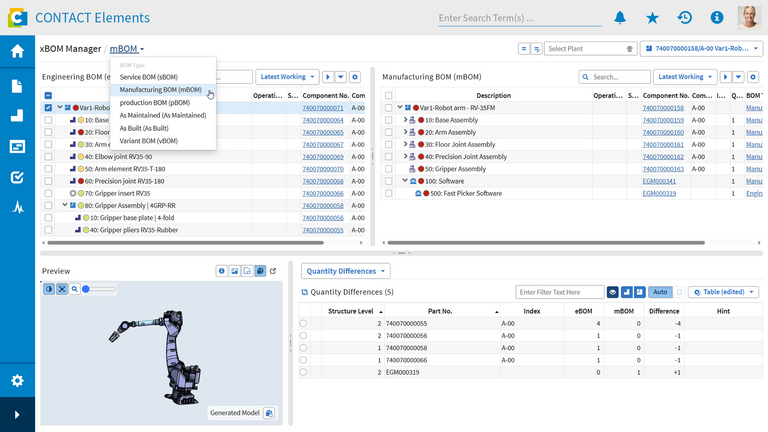
The xBOM Manager enables the comparison of engineering BOMs (eBOMs) with other structures such as service, spare parts and maintenance BOMs. This enables you to support follow-up processes in the product life cycle that extend beyond production. For example, you can document specific order BOMs or construction statuses of machines in operation and lay the data foundations for supplying the digital twin on the basis of CONTACT Elements for IoT.
Synchronize any BOM type
The xBOM Manager enables the comparison of engineering BOMs (eBOMs) with other structures such as service, spare parts and maintenance BOMs. This enables you to support follow-up processes in the product life cycle that extend beyond production. For example, you can document specific order BOMs or construction statuses of machines in operation and lay the data foundations for supplying the digital twin on the basis of CONTACT Elements for IoT.
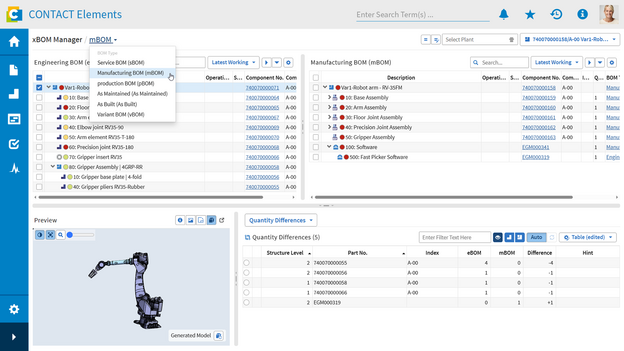
The xBOM Manager enables the comparison of engineering BOMs (eBOMs) with other structures such as service, spare parts and maintenance BOMs. This enables you to support follow-up processes in the product life cycle that extend beyond production. For example, you can document specific order BOMs or construction statuses of machines in operation and lay the data foundations for supplying the digital twin on the basis of CONTACT Elements for IoT.
Evaluate deviations directly in the 3D model
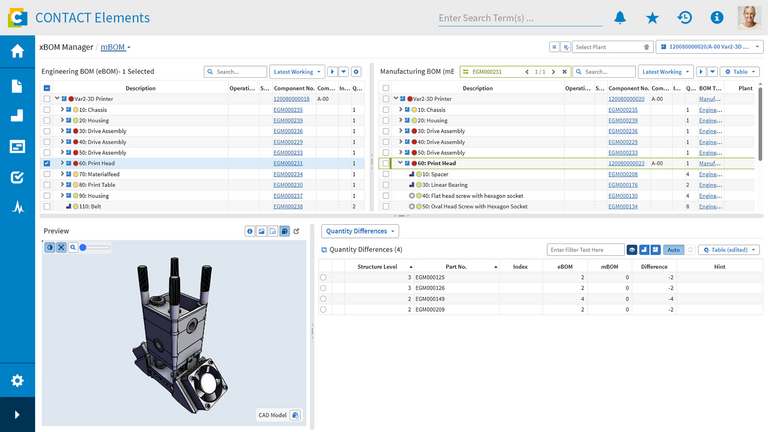
Combined with CONTACT Elements 3D Connect, the xBOM Manager supports the analysis of deviations. The 3D preview and visual navigation along the product structure facilitate evaluation and enable rapid, reliable corrections.
Evaluate deviations directly in the 3D model
Combined with CONTACT Elements 3D Connect, the xBOM Manager supports the analysis of deviations. The 3D preview and visual navigation along the product structure facilitate evaluation and enable rapid, reliable corrections.
Combined with CONTACT Elements 3D Connect, the xBOM Manager supports the analysis of deviations. The 3D preview and visual navigation along the product structure facilitate evaluation and enable rapid, reliable corrections.
Related Elements
Create product structures and architectures with confidence
Develop products that meet requirements
Establish mechatronic product structures for systems engineering
Configure variants using 150% structures
Manage bills of materials and ensure compliance
Utilize reliable interfaces between engineering and production
From virtual product to smooth start of production
Create transparency in the pre-series process
Effectively manage and cost-efficiently control production ramp-up
Plan with precision and on time using prototype BOMs
Document activities in prototyping and testing, and synchronize tools with production
Get better insights and make faster decisions with 3D product data
Design processes at the push of a button with model data
Use visual analyses and make decisions with the 3D cockpit
Enhance team collaboration by sharing model data
Leverage standards like 3D PDF, JT, and STEP for more possibilities
Accelerate product protection with digital mockups
Further information
Would you like to find out more about this topic? Choose one of the following information offers.