Bringing Smart Factory to reality
At the SPS 2023, CONTACT had again a strong presence and showcased its solutions for asset management, the Smart Factory, and data-driven services. Ahead of the automation fair, we talked with Kilian Bächle from our IoT team about how companies can achieve industrial digitization.
Industry 4.0 makes companies fit for the future – and in theory, nothing stands in the way of its implementation. Advancements in Artificial Intelligence (AI), edge computing, and industry standards for the intelligently connected factory and the digital twin are impressive. Cloud computing is more affordable than ever, and an increasing number of Internet of Things (IoT) solutions are entering the market. But how do companies make the right choice in this complex array of options?
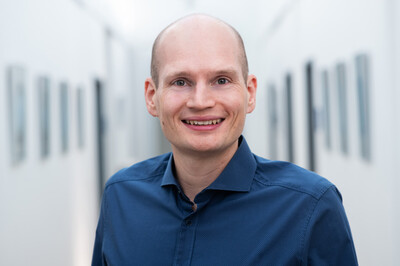
As Product Manager and Consultant for the open low-code platform CONTACT Elements for IoT, Kilian Bächle has kept a close eye on this rapid development for years. In this interview, he discusses perceived obstacles in industrial digitalization and outlines how companies can leverage data to automate their manufacturing or service business.
Kilian, most companies see the Smart Factory as a lucrative scenario. And yet, many of them don't act. What's the reason for this?
Probably because the buzzword "Smart Factory" sounds like an unattainable vision. However, when you approach the topic with a healthy dose of realism, it becomes clear that there are several steps on the way to digitalized manufacturing. Each step already creates added value and is therefore worth taking.
I'm sure that the majority of industry players have already tackled the topic. Most companies have at least implemented the first one or two steps, although the sequence and priorities of these measures may vary depending on sector and company.
It's important that the individual steps are taken at a pace suitable for the company, but that they are not thought of independently of one another – otherwise, isolated solutions may arise. It makes sense to define a digitalization strategy with clear goals and break it down into realistic subprojects to achieve a coherent big picture in the end. External support can help specify the necessary steps and assess their feasibility.
Can you give some examples of where companies can start?
My advice for companies is to first consider what they require to identify improvement potential and implement corresponding measures in the long term. The basis for this is evaluable information on the efficiency and quality of production, such as the top 5 reasons for downtime or scrap.
This foundation is established by collecting operational data and enabling digital feedback from factory staff, which provides the initial impetus for meaningful improvement measures.
Companies can start by documenting scrap reasons and digitizing paper-based processes such as shift or inspection protocols – to name a few easy-to-implement measures.
A bit more effort is needed to set up a digital twin of the operating equipment and record machine data there, optimize maintenance management, connect different plants, and collect globally transparent and uniform KPIs.
Analyzing machine data during production and linking it with the quality data of individual manufacturing processes reveals correlations that help quickly identify and address the root causes of problems.
Sustainability is a huge topic within the industry. What can the Smart Factory contribute to it?
Factories consume a significant amount of energy and raw materials. Savings in this area are valuable both in an economic and ecological sense.
An IoT platform can visualize the energy consumption of the machines, plants, and the manufacturing environment, such as hall temperature or lighting. Using this data and intelligent automation, companies can take efficient measures to minimize energy consumption in the production process. For example, the availability of energy-intensive assets can be linked to the production schedule. Whereas employees previously kept an industrial furnace permanently running for the sake of convenience, energy usage can now be adjusted to actual demand.
Capturing scrap reasons, in turn, enables targeted efforts to minimize defective parts, which saves valuable resources and reduces cost.
Thank you for the insightful conversation, Kilian.
The second part of this interview addresses the topic of "Smart Services". If you would like to meet Kilian Bächle at SPS 2023 or request a personal demo of CONTACT Elements for IoT, you can schedule an appointment here.
This video illustrates how thyssenkrupp Dynamic Components utilizes CONTACT Elements for IoT for global Manufacturing Operations Management (MOM).