Werner-von-Siemens Centre Maintenance Repair Overhaul 2.0
The research project aims to establish a flexible and individual Maintenance, Repair, and Operations (MRO) process chain for gas turbine blades using Digital Twins. This process chain should be capable of handling maintenance and repair measures in a demand-driven and cost-optimal manner. Various tools, such as inspection, simulation and AI models, are used for the corresponding automated diagnosis of geometrically complex turbine blades and damage prognoses. The MRO 2.0 project was already applied for in a previous first phase as part of the "Werner von Siemens Centre for Industry and Science" funding programme in Berlin and worked on during the period from January 2020 to December 2022. During this first phase of the project, the focus was on digitizing the execution of inspections and repairs on turbine blades. For this purpose, the IT infrastructure was established, and new data models for the service were conceived and integrated. The second phase aims to build upon these results and integrate a flexible service execution for the demand-driven design of inspection and repair measures within the Digital Twin.
- Project start: January 2023
- Runtime: 2 Years
- Funding amount: €8 million
- Number of partners: 10
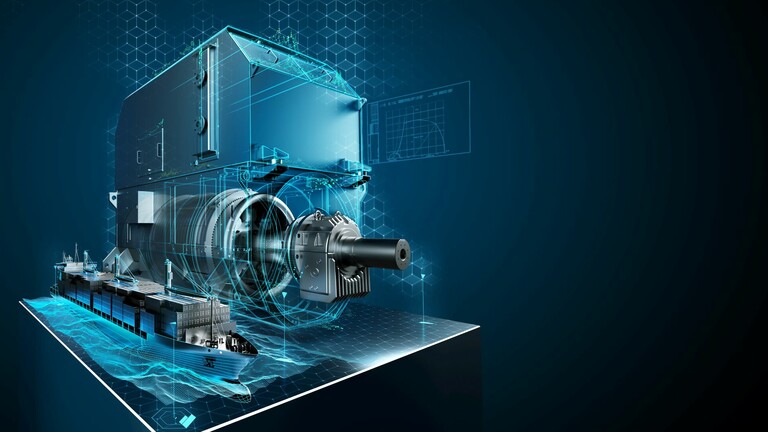
Objectives
The goal of the 2nd phase is to support the preceding inspection and service planning and to specify rough planning of the measurement and repair procedures, with a focus on human-machine interaction, sustainability and comprehensive networking in the Digital Twin.
CONTACT Research has set the goal in the project to further digitize the maintenance of gas turbine blades through digital twins. For this purpose, CONTACT is providing the CONTACT Elements development platform in the project and expanding it with new functions and methods:
◾ Conceptual design of a standardized data model for mapping inspection points and inspection plans with individual/flexible repair measures in digital twins.
◾ Automated derivation of repair actions from inspection results via the inspection and service actions catalogue.
◾ Analysis and conceptual integration of inspection models in CONTACT Elements.
◾ Development of a deployment pipeline for the deployment of AI and simulation models in digital twins in CONTACT Elements.
Objectives
The goal of the 2nd phase is to support the preceding inspection and service planning and to specify rough planning of the measurement and repair procedures, with a focus on human-machine interaction, sustainability and comprehensive networking in the Digital Twin.
CONTACT Research has set the goal in the project to further digitize the maintenance of gas turbine blades through digital twins. For this purpose, CONTACT is providing the CONTACT Elements development platform in the project and expanding it with new functions and methods:
◾ Conceptual design of a standardized data model for mapping inspection points and inspection plans with individual/flexible repair measures in digital twins.
◾ Automated derivation of repair actions from inspection results via the inspection and service actions catalogue.
◾ Analysis and conceptual integration of inspection models in CONTACT Elements.
◾ Development of a deployment pipeline for the deployment of AI and simulation models in digital twins in CONTACT Elements.
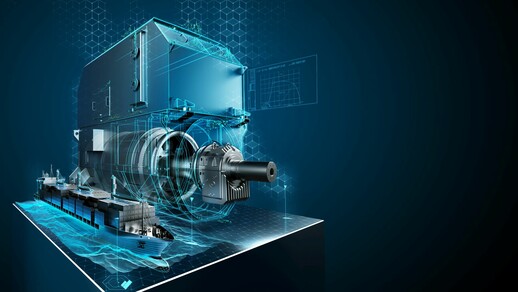
Objectives
The goal of the 2nd phase is to support the preceding inspection and service planning and to specify rough planning of the measurement and repair procedures, with a focus on human-machine interaction, sustainability and comprehensive networking in the Digital Twin.
CONTACT Research has set the goal in the project to further digitize the maintenance of gas turbine blades through digital twins. For this purpose, CONTACT is providing the CONTACT Elements development platform in the project and expanding it with new functions and methods:
◾ Conceptual design of a standardized data model for mapping inspection points and inspection plans with individual/flexible repair measures in digital twins.
◾ Automated derivation of repair actions from inspection results via the inspection and service actions catalogue.
◾ Analysis and conceptual integration of inspection models in CONTACT Elements.
◾ Development of a deployment pipeline for the deployment of AI and simulation models in digital twins in CONTACT Elements.
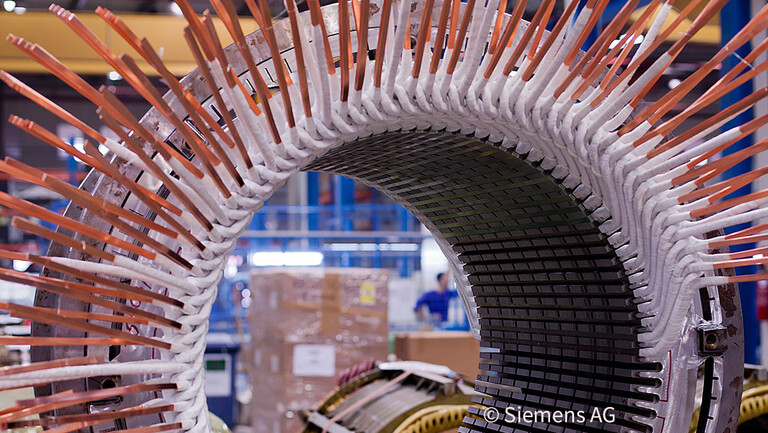
Motivation
Digitization is revolutionizing the way MRO activities will be conducted in the future, enabling a more efficient and precise maintenance of facilities, machinery, and components. By using digital technologies such as the Internet of Things (IoT), artificial intelligence (AI) and machine learning, companies can monitor the condition of their assets or components in real-time and develop predictive maintenance strategies. Digitization also offers the opportunity to automate and optimize MRO processes. In this way, it helps to accelerate maintenance and to service plants and products in such a way that they can be operated more efficiently and optimized for the specific need.
Motivation
Digitization is revolutionizing the way MRO activities will be conducted in the future, enabling a more efficient and precise maintenance of facilities, machinery, and components. By using digital technologies such as the Internet of Things (IoT), artificial intelligence (AI) and machine learning, companies can monitor the condition of their assets or components in real-time and develop predictive maintenance strategies. Digitization also offers the opportunity to automate and optimize MRO processes. In this way, it helps to accelerate maintenance and to service plants and products in such a way that they can be operated more efficiently and optimized for the specific need.
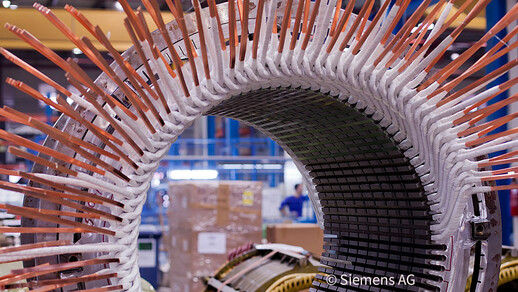
Motivation
Digitization is revolutionizing the way MRO activities will be conducted in the future, enabling a more efficient and precise maintenance of facilities, machinery, and components. By using digital technologies such as the Internet of Things (IoT), artificial intelligence (AI) and machine learning, companies can monitor the condition of their assets or components in real-time and develop predictive maintenance strategies. Digitization also offers the opportunity to automate and optimize MRO processes. In this way, it helps to accelerate maintenance and to service plants and products in such a way that they can be operated more efficiently and optimized for the specific need.
Project Partners
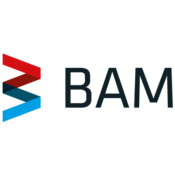
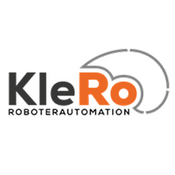

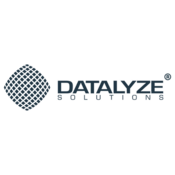
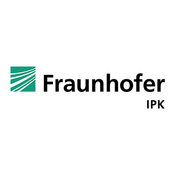

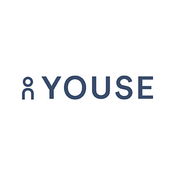
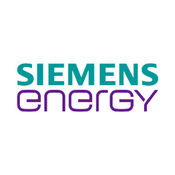
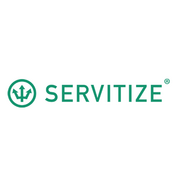
Contact for the Project
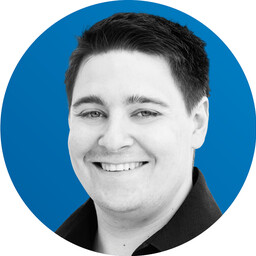
Projektingenieur IoT & Industrie 4.0
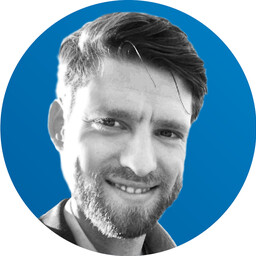
Project engineer IoT & Industry
This research and development project is funded by the European Regional Development Fund (ERDF) and supervised by the Investitionsbank Berlin (IBB).
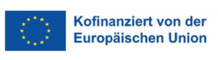
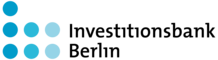