Industry 4.0: With data analytics to the perfect retrofit
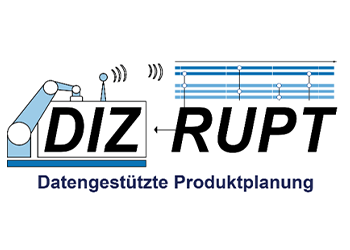
More and more machines are connected and transmit information on their operating status or error messages. A new research project aims to enable companies to profitably utilize this usage data in strategic product planning.
As part of Industry 4.0, the mechanical and plant engineering industry is equipping its new systems with modern sensor and communication technology. Manufacturers are also retrofitting more and more existing plants so that their customers can benefit from the advantages of digitization without having to buy expensive new machines.
Until now, companies have primarily used the operating data collected by industrial analytics methods in the area of service - for predictive maintenance, for example. However, systematic data analysis of product usage also promises important impulses for product improvement.
The joint project DizRuPt "Data-supported retrofit and generation planning in mechanical and plant engineering" was recently started with the aim of exploiting this central field of application for manufacturers.
The project
Machine and plant manufacturers often know too little about how customers really use their systems. They therefore base the strategic product planning on hypotheses that they determine through market research, feedback from customer service or personal meetings.
Industrial data analyses allow much more precise conclusions to be drawn about what current and future product generations should achieve. "Today, many delivered systems are more or less a kind of black box for the manufacturers with regard to their actual use by customers," says Thomas Dickopf, analyst at CONTACT Software. "We want to change this with new applications for Industrial Analytics”.
The systems engineer Dickopf is one of the CONTACT experts involved in DizRuPt. The aim of this research project is to create the organizational and technical prerequisites so that machine and plant construction can gain reliable information for strategic product planning on the basis of user data analyses and their interpretation.
Prof. Dr.-Ing. Roman Dumitrescu, head of the chair for Advanced Systems Engineering at the Heinz Nixdorf Institute of the University of Paderborn, coordinates the joint project, for which renowned partners from industry and science have joined forces. Besides CONTACT, the consortium includes the companies Diebold Nixdorf, Lasco, Weidmüller Interface and Westaflex, the Institute for Machine Tools and Factory Operation of the TU Berlin, the University of Applied Sciences Südwestfalen as well as Axoom as a further technology partner.
The solution
A smart plant or plant population provides vast amounts of data during operation, including valuable information for strategic product planning. Here, DizRuPt evaluates two different approaches for industrial analytics: the actual product usage and the identification of previously unknown correlations through explorative data analysis methods.
On the one hand, Industrial Analytics is intended to support companies in verifying their product hypotheses. For example, is the assumption that a basic function is only used by 8% of customers correct? If so, the manufacturer would have the option of no longer offering this in the next product generation or only at an additional charge.
On the other hand, a data analysis can show which components fail more often and why. One example are frequent defects in relation to the operating point of a machine. In both cases, such findings enable manufacturers to better decide whether to retrofit existing systems or to schedule certain functions for the next product generation.
With its Elements for IoT platform and the digital twin, CONTACT Software will implement prototype analytics applications that will be tested by DizRuPt's industrial partners. This results in data-based methods and new apps for product management in CIM Database PLM that systematically support feature planning.
Conclusion
DizRuPt will enable mechanical and plant engineering companies to better understand their customers through Industrial Analytics and to carry out targeted retrofit and generation planning.
In the project concrete demonstrators are realized which are of interest for the entire manufacturing industry. "The possibilities to benefit from operating data are enormous," says Prof. Dumitrescu. "Especially companies that have so far been producing traditionally get the chance to continuously improve their products or develop completely new offers".
The results of DizRuPt will generate high benefits, last but not least through their transferability to other business sectors such as vehicle construction.
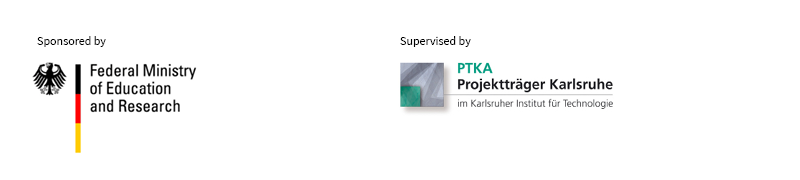