Innovative SLS-Simulation am Digital Twin
Innovative SLS-Simulation am Digital Twin
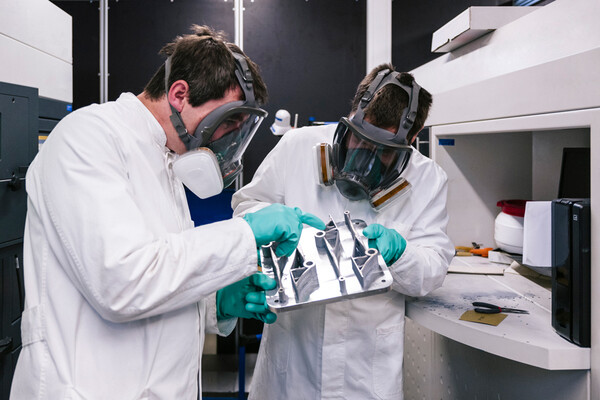
In den nächsten Jahren muss die Industrie ihre Emissionen drastisch reduzieren. Doch noch sind manche Alternativen zu Kohle, Öl oder Erdgas wie beispielsweise „grüner“ Wasserstoff nicht anwendbar: Ein derartiger Brennstoff erzeugt zu hohe Temperaturen für gängige Gasturbinen. Dieses Problem will ein Forschungsteam am Berliner Werner-von-Siemens Centre for Industry and Science lösen. Im Projekt „Hochtemperatur-Anwendungen“ entstehen Bauteile mit innovativen Kühlkonzepten, deren Funktion und Material auf Temperaturen von weit über 1000 Grad Celsius und eine lange Lebensdauer ausgelegt sind.
Die Projektpartner setzen auf Additiv Manufacturing (AM) Verfahren, um die nötige Freiheit beim Design wie auch bei der Erprobung von geeigneten Werkstoffen zu haben. Die späteren Prototypen werden per selektivem Lasersintern (SLS) hergestellt. Damit der 3D-Metalldruck das gewünschte Resultat liefert, sind viele Parameter wie beispielsweise die Leistung, der Fokus und die Bewegung des Lasers zu berücksichtigen. CONTACTs Ziel ist es, den Aufwand für die optimale Einrichtung der SLS-Maschine signifikant zu verringern.
Dazu digitalisieren CONTACTs Industrie 4.0 Experten die gesamte AM-Prozesskette über die Elements for IoT Plattform. Dies gibt ihnen die Möglichkeit, sich der Lösung mit verschiedenen Methoden zu nähern: Durch wiederholte Simulation eines Fertigungsvorgangs mit Live-Parametern aus dem realen Prozess. Durch Analysen der Simulationsdaten und der Sensorwerte aus der Produktion. Und durch den Abgleich der virtuellen Ergebnisse mit den realen Parametersätzen. Der Digital Twin und neue Ansätze aus der Analytik helfen dabei, das Simulationsmodell zu erproben und Schritt für Schritt zu verbessern.
Die Projektergebnisse sollen nicht nur dazu beitragen, den CO2-Ausstoß von Kraftwerken und im produzierenden Gewerbe zu senken. Die Industrie profitiert auch von neuen IoT-Verfahren und Werkstoffen für den 3D-Metalldruck. In der Luft- und Raumfahrt, dem Automobilbau, der Medizintechnik und verwandten Branchen lassen sich so komplexe Metallbauteile ohne traditionelle Fertigungstechniken wie Zerspanen, Fräsen oder Vakuumgießen deutlich schneller und kostengünstiger herstellen.
Konsortium
Siemens AG (Koordination), vier weitere Industriepartner sowie verschiedene Institute der Bundesanstalt für Materialforschung und –prüfung, der Fraunhofer-Gesellschaft und der TU Berlin
Ihr Ansprechpartner:
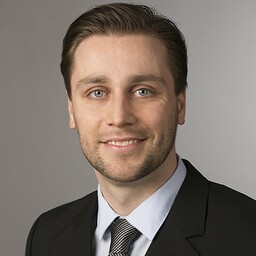
Projektingenieur PLM & Industrie 4.0, Engineering Transformation Team
Gefördert durch:
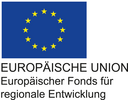
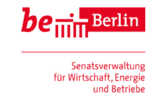